
INVENTIONS
HVP Shielding

The ASM Mercury in low earth orbit will need of a layer of exterior shielding
to protect against high velocity particles. We will use the shielding invented by AeroSpace Meridian team members Andrew Olafsrud, lead inventor, and Austin Pham, secondary inventor. This shielding is USPTO patented in January 2021 under the name SELF-HEALING SHIELD CONFIGURED TO PROTECT AN ENVIRONMENT FROM HIGH VELOCITY PARTICLES and previously protected by a provisional patent filed by our invention team. High velocity particles (HVPs) are any particles that travel at a higher speed than two kilometers per second; however, the normal speed for a high velocity particle is considered twenty kilometers per second. Despite their small size, the velocity of the particles cause them to have a high kinetic energy, rendering them capable of causing substantial amounts of damage. HVPs are also very common with tens of millions of them estimated to be in earth’s orbit; therefore, an impact with an HVP is an eventuality. The damage an impact by an HVP can cause necessitates shielding to protect against breaching the interior or damaging any components. The ASM Mercury shielding will combine three primary components to create a highly durable protection for the station. The components are: Dyneema®, spheroids of four different diameters, and polyethylene glycol with suspended silica particles. These will all be assembled into individual shield panels measuring 55 X 55 X 6.5 cm in dimensions.

Dyneema® is a strong synthetic aramid fiber, similar to Kevlar®, with a few differences in operational temperature, reaction to water, and strength. Dyneema® is approximately fifteen times stronger than iron, compared to Kevlar® which is five times stronger. Additionally, Dyneema® is hydrophobic, which means that it repels water without absorbing it; this is in contrast to Kevlar®, which absorbs water. Because of the presence of liquid polyethylene glycol, the Kevlar® will be unfit for use in the shielding design as it will start to absorb and leak the fluid. Due to Dyneema®’s nature as a type of fabric, it is far more flexible and lighter than iron, making it the best choice for the shielding design. The Dyneema® will be used as the walls of the shielding panels. To provide the first line of defense against the impacts of the high velocity particles and keep the weight low, the shield walls are 4 mm in thickness. Each shield panel will be filled with approximately 50% in volume with spheroids. These will be produced in four different sizes: 0.17 mm (67%), 0.7 mm (22%), 3 mm (7.6%), and 1.26 cm (3.4%). These relative sizes and quantities were selected to correspond to the HVP flux, HVP potential puncture diameter, and shear-thickening fluid flow for self-healing. The remaining volume of the shield panel will be filled with the dilatant fluid polyethylene glycol (PEG). PEG has been chosen because when it contains suspended silica particles, it becomes a shear-thickening fluid. Such a fluid, when exposed to pressure, increases its viscosity until it is almost solid. Shield panels are placed on the exterior of the space station. For those shield panels placed perpendicularly to the axis of rotation of the space station, the spheroids will remain against the outer shield panel wall due to the artificial gravity of the rotation. For all other shield panels, the spheroids will be held against the outer wall of the shield panel by an internal viscoelastic mesh which passes through the center of the shield panel.



An HVP impacting a shield panel will disintegrate. Upon impact, these spheroids will absorb the kinetic energy, impacting against each other, deflecting the kinetic energy
radially and laterally. In turn, their motion will be dampened by the dilatant fluid. The kinetic energy will cause the polyethylene glycol to harden, absorbing the energy. This
absorption will work in tandem with the spheroids to provide optimal protection. The impact puncture in the Dyneema® will start to degrade the strength of the shield panel; the spheroids have been designed to counteract this reaction. The spheroids will move towards the puncture due to both the rotational artificial gravity and the vacuum in
space. The spheroid diameters ensure that large spheroids cannot block access of smaller spheroids towards a puncture. Once a spheroid has reached the puncture, it will lodge into the puncture, clogging it, while also providing structural support to the weakened area.
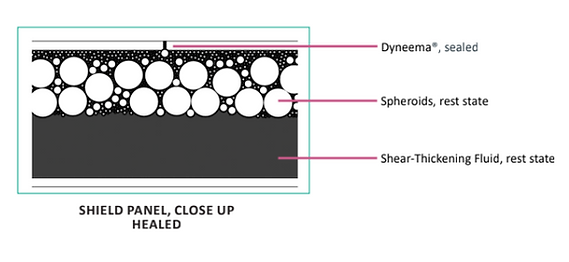
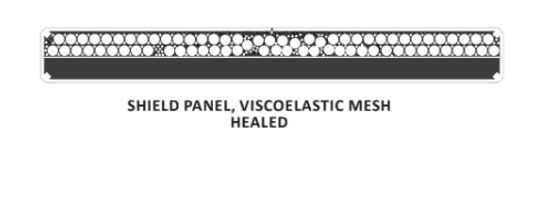
The Gravity Reduction Trolley
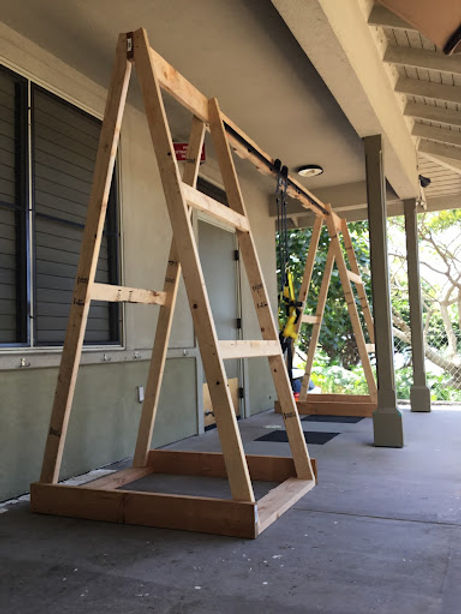
The Gravity Reduction Trolley was originally designed by the lunar habitat shoe team to simulate lunar gravity to test the shoe and flooring prototype. Using the trolley to test the prototype was extremely helpful and convenient, allowing the team to design shoes and flooring suitable for lunar gravity. It consists of a rail supported by two A-frame towers. The pulley system supports the harnessed user with bungee chords that can be adjusted to simulate lessened gravity. The AeroSpace Meridian team anticipates using the Gravity Reduction Trolley to simulate different gravities in the future for upcoming projects.
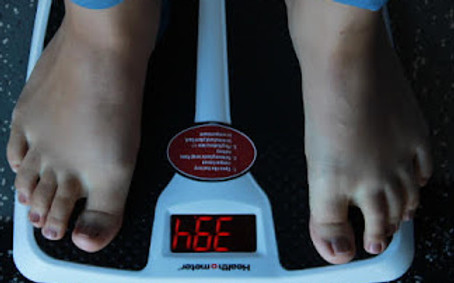